Формування клеєного бруса є складним, тривалим і багатостадійним процесом. Природно, чим більше технологічних операцій необхідно виконати для виготовлення кінцевої продукції, тим вище її додана вартість. А висока додана вартість - це рентабельність виробництва. Поряд з цим необхідно враховувати і зворотний закономірність: чим більше операцій, тим вище ймовірність отримання шлюбу.
Клеєні матеріали з цільної деревини в основному використовуються як несучі будівельні та столярні конструкції. У виробництві клеєного бруса для домобудування вихід продукції становить від 20 до 30% від обсягу колод.
Низький об'ємний вихід обумовлюється відходами та втратами деревини при обробці, що включають:
- до 50% - обсяг відходів колод при формуванні пиломатеріалів;
- до 15-20% - обсяг вад в пиломатеріалах, які необхідно вирізати;
- до 4-7% - втрати на обробку в розмір по перетину (стругання) матеріалів до і після лінії зрощування;
- до 6% - безповоротні втрати матеріалу на усушку;
- втрати, що виникають при торцовке пиломатеріалів і бруса в розмір по довжині; залежать від специфікації готової продукції і можуть становити до 8-10%.
При вибракування всього одного кубометра клеєних конструкцій фактичні втрати складають близько 4 м 3 пиловочного колод (3-4 дерева віком стиглості). При такому виході готової продукції на перший план виходить забезпечення контролю якості матеріалів і виробів на всіх етапах технологічного процесу.
Розглянемо кожен етап докладно, щоб визначити, яким чином доцільно організувати і реалізувати роботу, покликану забезпечити контроль якості виготовляється вироби.
етап перший
На цьому етапі виробникам необхідно визначитися з вибором сировини для виготовлення клеєних конструкцій. На безлічі невеликих підприємств вважають за краще використання покупних пиломатеріалів, обходячись без власної ділянки лісопиляння. Зарубіжний досвід показує життєздатність такої моделі, однак її не завжди можна реалізувати в російських умовах. За кордоном пиломатеріали, що формуються в лісопильному цеху, упорядковано за допомогою силових і акустичних установок для визначення їх фізико-механічних властивостей, що є обов'язковою умовою їх використання у виробництві несучих клеєних конструкцій. Проведення такого сортування дозволяє не тільки гарантувати властивості міцності, а й економити пиломатеріали. За її результатами визначається місце розташування вад будови деревини, які впливають на якість і повинні бути видалені (вирізані). Слід також зазначити, що для виготовлення клеєних конструкцій доцільно використовувати пиломатеріали радіального і напіврадіального розпилу, великий вихід яких можливий тільки при реалізації спеціальних схем розкрою колод, що не завжди вигідно виробнику пиломатеріалів.
Виконуючи розкрій пиловочного колод, виробники клеєного бруса мають можливість випилювати пиломатеріали з різних зон колод - тих, де деревина з необхідними властивостями, пріоритет яких визначається в залежності від виду використовуваного сполучного і призначення клеєних елементів. Тим самим скорочуються втрати деревини на відбраковування пиломатеріалів з невідповідними вимогам технології властивостями.
Виробники клеєного бруса, які не забезпечують виробництво власними пиломатеріалами, а купують їх, змушені організовувати ділянку сортування пиломатеріалів за якістю і нахилу волокон деревини. Як правило, створення такої ділянки передбачається на етапі проектування підприємства.
етап другий
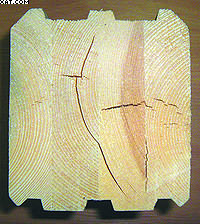
Мал. 1. розтріскування клеєного
бруса в торцях [1]
Наступною операцією, в ході якої формується більшість експлуатаційних властивостей майбутніх клеєних конструкцій, є сушка пиломатеріалів.
Багато виробників клеєних дерев'яних конструкцій в прагненні збільшити обсяг виробництва не хочуть використовувати для підготовки якісної деревини м'які режими, оскільки так збільшується тривалість сушіння.
Існує думка, що клеєний брус не схильний до викривлення, але це вірно тільки в тому випадку, якщо сушка виконана в м'якому режимі і після неї проведено кондиціонування пиломатеріалів для вирівнювання вологості і внутрішніх напружень, а також за умови правильного складання ламелей в брусі.
Сучасні клеї здатні склеювати деревину з вологістю до 15%, однак їх застосування не гарантує цілісності клейового з'єднання і стабільності форми продукції при порушенні технології сушіння і подальшої релаксації напружень, що виникають в деревині (рис. 1).
етап третій
На цій стадії виробництва виконується підготовка поверхонь ламелей до склеювання.
Відомо, що поверхня деревини поступово «старіє» і втрачає здатність до склеювання (зменшується число вільних радикалів, здатних взаємодіяти з клеєм), тому виробництво має бути організовано таким чином, щоб не пізніше ніж через півзміни (3-4 години) ламелі, оброблені в розмір по перетину на стругальних (поздовжньо-фрезерних) верстатах, надходили на ділянку склеювання.
«Старіння» деревини супроводжується підняттям ворсу і погіршенням змочуваності поверхні клеєм, що веде до збільшення витрати клею при нанесенні вулицями або пензлем. В результаті не тільки знижується адгезионная здатність деревини, а й зростає товщина клейового шару, що також негативно позначається на міцності клейового з'єднання.
Збільшення товщини клейового з'єднання може бути також викликано кінематичними нерівностями на поверхні ламелей, що виникають при їх обробці (рис. 2).
Висоту (h) і довжину (l) хвилі визначають за формулами (1), де h - висота хвилі, мм; l - довжина хвилі, мм; R - радіус ріжучої кромки леза циліндричної фрези, мм, і (2), де U - швидкість подачі, м / хв; n - частота обертання шпинделів, хв-1; z - число ножів, шт.
За даними компанії Leitz [2], для досягнення балансу між якістю обробки поверхні ламелей і раціональним режимом роботи ріжучого інструменту необхідно забезпечити довжину кінематичної хвилі 1,3-1,7 мм (рис. 3). У виробничих умовах обгрунтування необхідних параметрів роботи обладнання може бути визначено експериментальним шляхом, виходячи з властивостей оброблюваної породи деревини і інструменту.
Довжина і висота кінематичних нерівностей залежать від виду і ступеня затуплення ріжучого інструменту, а також від швидкості подачі і різання.
Крім збільшення товщини клейового з'єднання за рахунок утворення порожнин через кінематичних хвиль між склеюваних поверхнями відбувається зміна параметрів роботи обладнання, що також чинить негативний вплив на якість його роботи (рис. 4) і, відповідно, на якість підготовки поверхонь, що склеюються [3].
етап четвертий
На цьому етапі проводиться формування клеєного бруса. Досить поширена помилка на сучасних підприємствах: при складанні ламелей в брус вкрай мало уваги приділяється орієнтації ламелей щодо направлення волокон деревини.
Ламелі, як правило, візуально сортують тільки за якістю, без урахування місця їх випилювання з колоди, хоча формоустойчивость бруса в умовах експлуатації забезпечується саме за рахунок різного напряму волокон деревини в суміжних шарах, що необхідно для зниження впливу анізотропії деревини.
Конструкція бруса в поперечному перерізі повинна відповідати правилам симетрії і складатися з непарної кількості ламелей для зменшення напружень, що виникають при затвердінні пов'язує і в результаті усушки і розбухання (такі напруги можуть виникати також при експлуатації бруса, що працює на вигин).
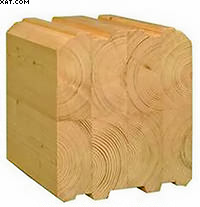
Мал. 5. Склеєний по кромці і пласти
брус з виходом серцевини на
лицьові пласти
При використанні в процесі виготовлення бруса парного числа ламелей максимальні дотичні напруження припадають на клейове з'єднання, як правило, працює на сколювання гірше, ніж цільна деревина.
При укладанні ламелей необхідно забезпечити їх складання таким чином, щоб в якості лицьових не використовувалися серцевинні дошки, орієнтовані серцевиною назовні (рис. 5).
Під впливом температурно-вологісних змін зовнішнього середовища і внутрішньої напруги деревини в ламелях (особливо при товщині більше 33 мм) може відбуватися відшарування і випадання серцевинною трубки з бруса в процесі його експлуатації.
Відповідно до ГОСТу 20850-84 «Конструкції дерев'яні клеєні. Загальні технічні умови »товщина склеюваних шарів в клеєних елементах повинна становити 20 ± 1 мм і 33 ± 1 мм, на підставі чого виробники беруть допуск на розмір рівним 2 мм - навіть при виготовленні ламелей нестандартних товщини і ширини.
Різнотовщинності ламелі, які формально знаходяться в полі допуску по товщині, досить складно склеювати, оскільки для забезпечення необхідної міцності клейового з'єднання необхідно забезпечити контакт між склеюваних поверхнями, що, з огляду на велику кількість ламелей в пресі, потребує докладання підвищеного тиску.
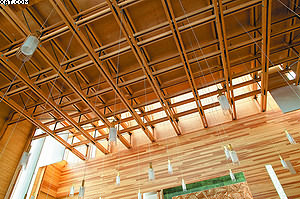
Крім цього, внаслідок різнотовщинності ламелей при їх склеюванні в деревині виникає внутрішня напруга, викликані нерівномірним стисненням по товщині і здатні привести до руйнування клейового з'єднання.
Не менш важливим моментом технологічного процесу є забезпечення сталої ширини пиломатеріалів. При склеюванні бруса по товщині тиск прикладається до пластям пиломатеріалів.
Для формування бруса необхідної геометричної форми пакет ламелей попередньо фіксується за допомогою фронтальних притисків, які передають тиск на кромки пиломатеріалів. При склеюванні зафіксованих фронтальними притисками ламелей різної ширини може відбуватися їх зміщення (рис. 6), в результаті якого при додатку тиску до пластям не буде забезпечено контакт між склеюваних поверхнями.
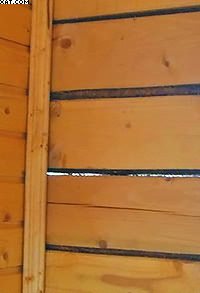
Мал. 7. Щілини між брусами з
дефектами форми [1]
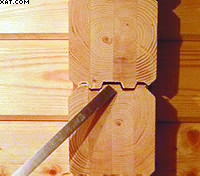
Мал. 8. Щілини між брусами з
дефектами форми [1]
Показники міцності клейового з'єднання при сколюванні на різних ділянках довжини бруса будуть різними [4], і залежать вони не тільки від фізико-механічних характеристик, що склеюються ламелей, щільності їх контактних шарів, але і від жорсткості притискної балки преса і числа циліндрів, передавальних тиск на склеювані заготовки. Тиск пресування в залежності від тиску в системі може бути визначено за формулою (3), де Pр.ж - тиск робочої рідини в пресі, МПа; F - площа склеюваної поверхні, м 2; n - число i-х циліндрів.
Створення якісного клейового з'єднання залежить не тільки від умов підготовки ламелей, а й від сполучного. При приготуванні і нанесенні клею необхідно витримувати в цеху задані виробником клею температурно умови, оскільки вони впливають на життєздатність пов'язує і тривалість відкритої / закритої витримки.
При використанні багатокомпонентних клеїв, підготовлених до нанесення з порушеннями технології, або в разі їх застосування після закінчення терміну життєздатності затвердіння може статися передчасно, і тільки між склеюваних поверхнями - без проникнення в контактні шари деревини. Подібні дефекти склеювання досить складно розпізнати в виробничих умовах без проведення випробувань клеєного бруса по всій його довжині за допомогою рентгенографії або ультразвуку. Виконати випробування за допомогою методів руйнівного контролю в даному випадку неможливо. Руйнування таких клейових конструкцій, як правило, відбувається під час їх експлуатації в результаті зміни температурно-вологісних умов, що тягнуть за собою зміну розмірних характеристик ламелей, які при цьому не стримуються належним чином клейовими з'єднаннями.
При склеюванні заготовок в пресі клейове з'єднання зазвичай не встигає набрати необхідну міцність, для досягнення якої необхідно забезпечити витримку бруса після пресування. Тривалість витримки визначається типом сполучного за рекомендаціями виробника.
Витримка здійснюється на подстопних місцях, основною вимогою до яких є прямолінійність підстави, що не дозволяє брусу деформуватися під дією власної маси.
При складанні будинків з деформованого клеєного бруса утворюються щілини (рис. 7, 8).
етап п'ятий
Заключним етапом процесу виробництва клеєного бруса є формування сполучних елементів.
Після склеювання і технологічної витримки необхідно виконати профілювання бруса для формування монтажних пазів і гребенів, а також порожнин, в які вкладається утеплювач.
На цій стадії може відбуватися зниження якості бруса за рахунок розтину смоляних кишень і випадання сучків, які були непоміченими або невірно визначені на попередніх стадіях технологічного процесу.
Для їх закладення доцільно використання різних вставок у формі «човників» або «пробок» з цільної деревини.
Розкрилися дефекти можуть бути видалені і при формуванні сполучних лап і чашок, а також при торцовке бруса.
Анатолій ЧУБИНСЬКИЙ,
д-р техн. наук, проф.,
Олександр Тамбов,
канд. техн. наук, доц.,
СПбГЛТА ім. С. М. Кірова
джерела:
Лісопромисловий комплекс, лісова галузь, лісовий комплекс, лісозаготівельний комплекс, лісопромислова галузь, лісопильна промисловість, ліс, лісозаготівельна галузь, лісова промисловість, деревообробна промисловість. Статті про лісозаготівлі, деревообробки, біоенергетиці, дерев'яному житловому будівництві, виробництві деревних плит, лісозаготівельної техніки, лісопильному та деревообробному обладнанні.