Маса зразків-вкладишів становила при перетині 60 X 60 мм 25-27 кг, а при перетині 80 X 80 мм 48-49 кг. Вивантажувані з печі вкладиші охолоджували в воді (в баку для замочки пічного інструменту), зразки очищали від окалини до і після нагрівання металевими щітками і зважували на точних вагах (призначених для перевірки гир) 1-го класу з найбільшою допустимою навантаженням 50 кг і з похибкою при граничному навантаженні, що не перевершувала ± 500 мг.
Значення чаду, виражене у відсотках, може бути в першому наближенні прийнято однаковим у заготовок і зразків вкадишей.
Однак і при цьому методі визначення значення чаду є відмінності в умовах нагріву зразків і заготовок, що призводять до деяких неточностей, а саме: відношення повної поверхні коротких зразків до їх масі (за рахунок торців) більше, ніж у довгих заготовок; зокрема за рахунок торців відношення відкритої поверхні, що омивається продуктами згоряння, до маси зразків більше, ніж у заготовок. Таким чином, угар у зразків-вкладишів повинен бути трохи більше, ніж у заготовок.
Якщо в процесі досліджень оцінити різницю у величині чаду металу на поверхнях зразків, які омиваються і неомиваемих продуктами згоряння (наприклад, по товщині окалини), то одночасно користуючись даними про загальний угарі зразків (певними зважуванням), можна при розрахунку значення чаду заготовок внести деякі поправки, що дозволяють уточнити це значення.
При визначенні чаду на заготовках, що гріються у зазначеній вище методичної печі, розрахунковими поправками встановили, що між значеннями чаду заготовок у3 і чаду зразків-вкладишів (УГБ) існувала наступна зв'язок:
Слід також мати на увазі, що заготовки завантажують в піч з невеликим шаром первинної прокатної окалини, яка в якійсь мірі захищає поверхню і трохи зменшує чад заготовок. Спостереження Центроенергочермета, проведені одночасно над зразками-вкладишами, попередньо очищеними (металевими щітками) від окалини і неочищеними, показали, що угар у неочищених зразків (уН.0) був менше, ніж у очищених (у0), і становив
Цю обставину слід враховувати, коли визначають величину чаду заготовок в печі на підставі спостереження за чадом зразків, попередньо очищених від окалини.
Втрати металу від чаду, які значаться в звітності заводів, характеризують зазвичай суму чаду: в печі, при транспортуванні до стану, в процесі прокатки і при подальшому охолодженні металу. У процесі прокатки, коли поверхню металу збільшується, зростає також значення чаду. Безпосередньо в печі втрати від чаду бувають значно менше. Наприклад, величина чаду, певна спеціальними спостереженнями в методичних печах з монолітним подом, які обслуговують дрібносортний і дротяний стани, не перевищувала 1% і становила менше половини загального чаду, що значиться за звітності заводу, що слід пояснити додатковим окисленням металу після видачі його з печі.
Правильне визначення величини чаду металу, що відбувається безпосередньо в печі, має велике значення. На підставі цієї величини можна судити про економічну доцільність застосування тих чи інших способів зменшення чаду і, зокрема, безокслітельного нагріву.
З факторів, що впливають на величину чаду (температура, атмосфера в печі, та ін.), Найбільше впливає тривалість перебування металу в печі (при високій температурі). Наприклад, за спостереженнями, проведеними на методичній печі, де гріли сляби, при форсуванні темпу роботи і перебування металу в печі протягом 2 ч товщина окалини становила 2 мм, що відповідало чаду 1,5%; при середньому темпі роботи і тривалості нагріву 3,5 год товщина її становила 2,6-3,0 мм, що відповідало чаду 2%; при тривалих простоях товщина окалини була 5,5-6,0 мм, що відповідало чаду 4%.
При звичайній роботі методичної печі з монолітним подом, яка обслуговує дротяний стан, нагрів заготовок тривав, як правило, 55-65 хв і угар при цьому становив 0,75-0,85%, а коли через простої тривалість нагріву підвищувалася до 2 2,5 ч, угар металу досягав 1,5-2,5%.
На методичної печі, де грілися злитки, товщина окалини при форсованому темпі роботи становила 2,5-3,5 ммv що відповідало чаду металу 1,1-1,6%; при середньому ході печі товщина окалини була 4-5 мм, що відповідало чаду 2%; а при тривалих простоях товщина окалини досягла 10 мм і більше, що вже могло призвести до розкриття підкіркових бульбашок в злитках і до шлюбу.
Наявність сірки в паливі збільшує окалинообразования і знижує температуру плавлення окалини. Так, наприклад, значно зросли труднощі експлуатації методичної печі через підвищений зростання пода томильной зони, коли застосовувався для її опалення змішаний газ замінили одним
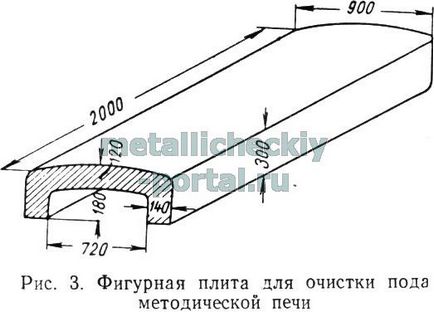
На багатьох методичних печах, де температура нагріву металу відносно невисока (1220-1250 ° С) і піч не працює форсовано, значна частина окалини забирається з монолітного пода в неоплавленном стані. Збирання її здійснюють шкребками з-під фігурної плити (рис. 3), проштовхується через піч кожні 2-3 зміни, а повне очищення поду від налиплого на нього шлаку із звільненням його від металу проводять раз на місяць і рідше. Однак не у всіх випадках вдається обмежитися зазначеним відносно легким методом видалення окалини. Особливо страждають від шлакообразования і інтенсивного зростання монолітного пода томильной зони печі, де гріються злитки спокійній стали з обрізає головною частиною (з низькоплавких включеннями) і печі тонколистових станів, де до температури нагріву металу пред'являються підвищені вимоги. Фігурна плита в цьому випадку допомагає менше і чистку пода з видаленням металу з печі виконують щотижня і частіше. Наприклад, при нагріванні зазначених злитків монолітний під протягом 3-4 діб роботи наростав на 300-600 мм. засоби для
механізації процесу очищення пода ще не знайдені, а приведення в задовільний стан пода, зарослого шлаком, являє собою важку і трудомістку роботу, для виконання якої на допомогу персоналу, який обслуговує піч, часто надсилають робочих з інших ділянок виробництва. При подвійній довжині заготовок (однорядною посадці довгих слябів, блюмів) накопичення шлаку на монолітному поді менше.
Чад металу дещо зростає при безпосередньому впливі факела на метал, а тому зменшення довжини факела в томильной зоні сприяє деякому зменшенню зростання подини.
Збільшена товщина засипки монолітного пода полегшує вибивання наростів. В результаті зменшення товщини цегляної кладки поду підвищують товщину його засипання магнезитовим порошком приблизно до 100 мм. Природно, що при цьому слід відповідно змінити розміри брусів, які закладаються в подину. Розміри шматочків магнезитового порошку зазвичай складають 2-5 мм. Більш дрібний порошок видувається при включенні пальників (особливо інжекційних) для розігріву пода, крім того, він в більшій мірі зварюється з подом і його важче відокремити від нього. При більшому порошку шлак, заповнюючи проміжки між шматками, сприяє утворенню трудноудаляємиє монолітів. Для полегшення очищення від шлаку нижньої камери зварювальної зони під її засипають коксової дрібницею розміром шматків 2-5 мм, товщиною шару 50 100 мм.
Чим коротше монолітний під томильной зони, тим менше необхідно затратити праці та часу для очищення його від наростів. У зв'язку з цим спостерігається тенденція до вкорочення монолітного пода в печах з нижнім нагрівом. Пристрій монолітного пода описано також в розділі 12 цієї глави.
Бувають випадки, коли в зв'язку з інтенсивним зростанням пода при нагріванні злитків методичні печі з бічної видачею металу переводили на рідке шлаковидалення. Цим значно полегшували працю по очищенню пода, але не виключали тривалих простоїв печі, обумовлених необхідністю звільнення пода від металу, підйому температури в томильной зоні і підтримки її на цьому рівні до розплавлення шлаку і спуску його в ківш.
Для відведення нерасплавівшіеся шлакових охолодей і горбів доводиться також користуватися ферросилицием або алюмінієвим порошком.
Рідкому шлаковидалення з нижньої камери зварювальної зони значно сприяє герметизація цієї камери. Зокрема, щоб уникнути охолодження поду від підсосу повітря в камеру, необхідно закласти вікна камери.