Метод сепарації палив є в даний час найбільш поширеним способом очищення палив від різних домішок і води.
Паливо з цистерни відстою перекачується з проходженням через фільтр і сепаратор в видаткову цистерну. У разі дуже вузьких палив може виявитися необхідним збільшити температуру попереднього нагрівання до ≈ 98 ° С в залежності від початкової в'язкості.
Все що випускаються сепаратори можна розділити за принципом очищення барабана від шламу на дві групи:
- з періодичної розвантаженням барабана від шламу;
- з безперервною розвантаженням барабана від шламу.
Відділення з палива механічних домішок і води відбувається в барабані сепаратора. Безперервно надходить в барабан забруднений нафтопродукт також отримує обертальний рух. Під дією відцентрової сили, яка в тарілчастих сепараторах перевищує в 4000 ÷ 8000 разів силу тяжіння, вода і механічні домішки, що мають велику щільність, ніж паливо відкидаються до стінок барабана, а очищений нафтопродукт - ближче до осі обертання. Протікаючи між тарілками барабана, він відводиться через кільцевий отвір у верхній частині барабана.
За способом очищення барабана від забруднень розрізняють сепаратори самоочищаються і з ручним очищенням.
Найбільшого поширення набули самоочищаються сепаратори фірми «Лаваль» (Швеція), «Вестфалія» (ФРН), «Титан» (Данія). Відходи сепарації скупчуються в грязьових цистернах, а потім видаляються в спеціальні ємності зберігання відходів.
На малюнку 10.2.1 показаний розріз барабана відцентрового сепаратора.
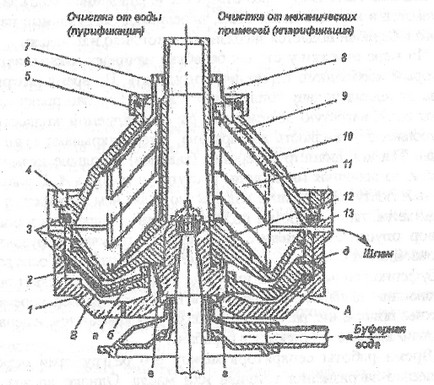
Мал. 10.2.1 - Конструкція відцентрового сепаратора.
1 - корпус барабана; 2 - затвор; 3 - ущільнювач кільця; 4 - гайка корпусу; 5 - гайка кришки; 6 - регулювальне кільце; 7 - водяна горловина; 8 - грязьова горловина; 9 - захисна тарілка; 10 - кришка барабана; 11 - пакет тарілок; 12 - тарелкодержатель; 13 - кільце.
Розвантаження барабана сепаратора від забруднень проводиться через пази, наявні на внутрішній циліндричній частині барабана. Під час сепарації ці пази перекриті затвором 2, який може переміщатися в вертикальному напрямку. У верхньому положенні він закриває розвантажувальні пази, в нижньому положенні - відкриває. Між затвором 2 і тарелкодержатель 12 знаходиться кільцева порожнина А, а між затвором і підставою корпусу - кільцева порожнина В. В затворі є отвір а. в корпусі барабан - отверстіеб. Внаслідок того, що отверстіеа знаходиться ближче до осі обертання, ніж отверстіеб. тиск води над затвором більше, ніж тиск води під ним.
Коли частота обертання барабана сепаратора досягає максимального значення (затвор при цьому знаходиться в нижньому положенні), для переміщення затвора; в верхнє положення відкривають кран в магістралі буферної води. По каналах в иг вода потрапляє в порожнині А і В. З порожнини А по каналуд вода витікає. У порожнині В вода залишається, а її надлишки випливають через отверстіеб. Тиском води затвор переміщається у верхнє положення, перекриваючи завантажувальні пази. Після цього в барабан подається забруднене паливо.
У міру очищення під стінами барабана починає накопичуватися шлам, який необхідно періодично видаляти. Під час розвантаження барабана від шламу подачу палива в барабан припиняють і подають воду, нагріту до температури сепарованого рідини, яка витісняє цю рідину з барабана, потім відкривають кран буферної води. Так як діаметр отворів (каналів) (в) більше діаметра отвору (г), то основна маса води надійде в порожнину (А). Оскільки в порожнину (А) надходить більша кількість води, ніж випливає з отвору (д), тиск над затвором в порожнині (А) стане вище, ніж в порожнині (В), і затвор опуститься в нижнє положення, відкриваючи завантажувальні пази. Відбудеться «постріл» - шлам вилетить з барабана. Після цього подача буферної води припиниться. Вода з порожнини (А) випливає з каналу (д) і тиск її падає. Тиск в порожнині (В) затвор переміщається у верхнє положення, розвантажувальні пази перекриваються, і сепарованого паливо подається в барабан. Час роботи сепаратора між його разгрузками визначається ступенем забруднення палива. Однак у всіх випадках розвантаження барабана слід виробляти до того, як його грязьове простір буде повністю заповнено шламом, в іншому випадку якість сепарування значно погіршується.
Залежно від ступеня забруднення сепарованого рідини водою або механічними домішками барабан може бути зібраний для роботи в режимі пурифікації (ліва частина рис. 10.2.1) і кларификация (права частина рис. 10.2.1). У першому випадку вода безперервно видаляється з палива через щілину в регулювальної шайби (гравітаційному диску). У другому ставлять глуху регулювальну шайбу, і вода видаляється з сепаратора тільки під час його розвантаження від шламу. Тому робота сепаратора на режимі кларификация можлива тільки при необводнених нафтопродуктах або за умови попереднього очищення їх від води на режимі пурифікації. В іншому випадку вода швидко заповнить весь грязьовий обсяг барабана і перекриє доступ чистого палива в межтарельчатого простір.
Для установки водяного затвора в правильне положення і забезпечення оптимальної сепарації важливо виконати наступне:
- вибрати гравітаційний диск відповідно до щільності рідини, її в'язкістю і витратою. Слід вибирати найбільший диск, який може використовуватися без порушення водяного затвора;
- забезпечити роботу сепаратора при постійній витраті;
- працювати при постійній температурі.
Для обробки важкого палива зазвичай використовують два сепаратора, для дизельного - один або два. Залежно від якості важкого палива обидва сепаратора включаються паралельно - робота в режимі пурифікації, або послідовно - перший сепаратор працює в режимі пурифікації, а другий - кларіфікатора. Після сепараторів накладених на них насосами паливо подається в видаткову цистерну.
При обробці важких палив в'язкістю від 120 до 380 мм 2 / с при 50 ° С сепаратор необхідно звільнити після роботи протягом 2-4ч. Для мазутів, в'язкістю до 600 мм 2 / с при 50 ° С максимальний час інтервалу між автоматичними вилученнями осаду не повинно перевищувати 1-2год.
У режимі кларификация сепаратор працює без водяного затвора, вихід води з сепаратора перекривається, і паливо очищається лише від механічних домішок. Зазвичай, кларіфікатор, що встановлюється послідовно з пуріфікатором, служить другим ступенем очищення.
При послідовній роботі сепараторів основна очищення здійснюється в пуріфікаторе (до 70% домішок збирається в ньому) і лише 10% припадає на частку кларіфікатора. Таким чином, роль кларіфікатора зводиться до видалення з палива залишилися в ньому більш дрібних частинок механічних домішок і ролі «сторожа» на випадок прориву механічних забруднень через пуріфікатор. При роботі на важких низькосортних паливах, одержуваних компаундированием залишків каталітичного крекінгу і вібреакінга з керосино-газойльових фракціями, сепарацію рекомендується здійснювати в режимі: два паралельно рабоатющіх на малій продуктивності пуріфікатора з послідовно включеним кларіфіктором. Ефективність очищення в цьому варіанті сягає 80-90%, в той час як в варіанті пуріфікатор-кларіфікатор вона становить 70%.
Вибір режиму сепарації набуває особливо важливе значення при очищенні палив, що містять алюмосилікатна дрібниця, яка може викликати буквально катастрофічний знос двигунів. Тут важливо сепарацію вести з малими подачами палива в сепаратори (15-20% паспортної) і по послідовній схемі з використанням кларіфікатора як останнього ступеня. При сепарації класичних мазутів (прямогонний залишків) можливі менш жорсткі вимоги до вибору режиму.
Відцентрові сепаратори забезпечують видалення домішок неорганічного походження з розмірами частинок 5 мкм і менше і органічного походження 7 мкм і менше, а також води (до слідів). Втрати горючої частини палива разом з отсепарирован водою і з осадом при видаленні не перевищують 1%, при очищенні залишкових мазутів - 3%.
Метод очищення палив (фільтрація, сепарація, гомогенізація) впливає на знос циліндрів. Дослідження фірми «Бурмейстер і Вайн» показали, що найбільш ефективним методом очищення палива в даний час є відцентрове сепарування. Для середньо - і високов'язких палив рекомендується комплекс засобів очищення: фільтри грубої очистки, відцентровий сепаратор, фільтри тонкого очищення. Фільтри, що видаляють забруднення, розміром до 1 мкм, на практиці відсутні, тому вони не можуть бути равноеффектівно сепараторам.
Для забезпечення задовільної сепарації в звичайних сепараторах щільність важких палив не повинно перевищувати 0,99 г / см 3 при 15 0 С. Максимальна різниця в щільності палива і води знаходиться в діапазоні 80-90 0 С. В'язкість палива при сепарації повинна бути 12-16 мм 2 / с (двотактні дизелі) і 9,5-14 мм 2 / с (чотиритактні дизелі).
Фірма «Альфа-Лаваль» рекомендує дотримуватися таких оптимальні співвідношення продуктивності сепаратора і температури сепарації залежно від в'язкості:
Для ефективної роботи сепараторів переважно виконувати наступні заходи:
- оптимально підбирати пропускну здатність сепаратора;
- підтримувати температуру сепарації в межах 2 0 С за допомогою автоматичного регулювання подачі пари на підігрівач;
- оптимізувати режим роботи сепараторів;
- уникати дросселирования і рециркуляції палива перед сепарацією.
Для гарного розпилювання палива його слід підігрівати перед уприскуванням. Необхідна температура підігріву залежить від відносної в'язкості застосовуваного палива. Тому важливим моментом у підготовці палива до спалювання є забезпечення необхідної в'язкості. Якщо для дизельних палив необхідність в підігріві для зниження в'язкості відпадає, то для важких палив попередній підігрів в парових або електричних подогревателях є обов'язковою умовою їх підготовки, тому що цим шляхом можна досягти необхідної в'язкості. Вплив в'язкості і стисливості на характеристику упорскування в залежності від конструкції паливної апаратури різному, але у всіх випадках воно в тій чи іншій мірі відбивається на якості розпилювання і подальшого згоряння палива. В'язкість, яка визначається силами внутрішнього зчеплення палива, і сили його поверхневого натягу безпосередньо впливають на розпад випливає з форсунки струменя палива. Ці сили прагнуть подовжити суцільну частина струменя і тим самим зберігати її цілісність, тому з їх збільшенням довжина суцільної частини струменя зростає, а тонкість розпилювання знижується.
Дослідним шляхом встановлено, що оптимум в'язкості палив для дизелів лежить в межах 12-20 мм 2 / с. Це значення в'язкості і має бути забезпечено відповідним підігрівом палива перед його використанням. Контроль за заданою в'язкістю і управлінням підігрівачем здійснює вбудований в систему подачі палива автоматичний регулятор в'язкості - віскозиметр. За ним встановлюють фільтри тонкого системи з тонкістю відсіву 6-15 мкм.
Щоб запобігти охолодження палива в системі подачі палива все труби ізолюються і забезпечуються паровими супутниками або обвиваються електронагрівальними елементами, а змішувальна цистерна забезпечується паровим змійовиком. При короткочасної зупинки двигуна циркуляційні насоси повинні продовжувати працювати, підтримуючи циркуляцію гарячого палива в замкнутому контурі.
Знос прецизійних пар топливоподающей апаратури залежить як від абразивних властивостей механічних домішок палива, так і від розмірів частинок. Найбільший знос викликають частинки забруднень розміром 6-12 мкм. Більші частинки не можуть відразу пройти в зазори, і таким чином, роблять менший абразивну дію. Основним технічним вимогою до фільтрів тонкого очищення є забезпечення відсіву частинок не крупніше зазначених найбільш небезпечних розмірів. Тому поряд з сепарацією в комплекс топлівообработкі входить фільтрування палива з використанням фільтрів грубої і тонкої очистки. Фільтри грубої очистки встановлюють перед усіма насосами: топлівоперекачівающімі, насоса, що підкачує сепараторів, бустерний і ціркуляціониимі), з метою попередження їх пошкодження при попаданні великих часток. Фільтри тонкого очищення встановлюють безпосередньо перед дизелями для захисту прецизійних елементів паливної апаратури від частинок механічних домішок, які не затриманих в сепараторі. Принцип дії фільтра заснований на відділенні від нафтопродукту забруднюючих домішок при його пропущенні через систему фільтрів перегородку, розміри осередків якої менше розмірів відфільтровує частинок. Найбільший розмір часток забруднень, що пропускаються фільтром, визначає тонкість відсіву. За цим показником є три групи фільтрів очищення палива:
- попередньої - для запобігання паливної системи від потрапляння випадкових великих забруднень (фільтри перед паливо-перекачувальними насосами);
- грубої - для видалення з палива частинок, розміром більше 40 мкм;
- тонкої - для видалення домішок, розмірами більше 6-15 мкм, а при застосуванні паперових елементів - більше 4-5 мкм.
Фільтр характеризується також коефіцієнтом очищення і ступенем фільтрації, яка представляє собою відношення маси віддалених домішок до її початкового значення:
де - маса домішок, що залишилися в продукті, що пройшов фільтрацію;
- маса домішок її початковому значенні.
На судах застосовують фільтри і самоочищаються фільтраційні установки. Залежно від принципу дії фільтруючі елементи можуть бути поверхневими, або об'ємними (ємнісними). У поверхневому фільтрі паливо очищається шляхом осадження домішок на поверхні елементів, крайках осередків, або щілин. В якості фільтруючого матеріалу використовують сітку, листову папір, тканину або фільтруючий елемент утворюється пластинками, витками дроту або стрічки (щілинні фільтри).
В об'ємному фільтрі нафтопродукт пропускається через фільтруючий матеріал, що містить безліч каналів і пор, в яких і відкладаються забруднюючі домішки. Для виготовлення об'ємних елементів використовують фетр, деревоволокнисті матеріали, металокераміку, пористу бронзу. Об'ємні фільтри на відміну від поверхневих здатні утримувати велику кількість бруду, мають більш високий коефіцієнт фільтрації і не здатні до раптового засмічення. Мінімальний термін служби будь-яких фільтруючих елементів через забивання їх асфальтосмолисті сполуками при фільтрації важких палив, не спроможність відділення води, потреба в ручному очищенні - послужили серйозною перешкодою до використання подібних фільтрів на сучасних судах. На зміну їм прийшли самоочищаються фільтраційні установки, що мають, в порівнянні з сепараторами, істотні переваги: малі енерго- і трудовитрати по їх обслуговуванню; можливість автоматизації; простоту конструкції і більш високу надійність в роботі; незалежність процесу очищення від різниці щільності палива і видаляються з нього частинок механічних домішок; менші втрати горючої маси.
Гомогенізація палива полягає в гідродинамічному обурення паливної середовища, в результаті якого в середовищі виникають кавитационні зони. Закривання кавітаційних каверн супроводжується локальними гідравлічними ударами високої потужності, що руйнують не тільки желеподібні згущення, але і тверді агломерати. В результаті паливо стає гомогенним, смоли рівномірно розподіляються в паливній середовищі, тверді частинки звільняються від «смолистої шуби», а глобули води диспергують.
Таке паливо сепарується і фільтрується з мінімальними втратами горючої частини. Гомогенізоване паливо має підвищену абразивністю, в зв'язку з чим його необхідно пропускати через ФТО. У практиці знаходять застосування гомогенізатори наступних типів: гідродинамічний, вібромеханіческій, ультразвукової, вихровий і ін.
Гомогенезатори не видаляють механічні домішки, золу і асфальтові включення, а зменшують розміри знаходяться в паливі частинок різних включень до безпечних для двигуна розмірів.
Використання гомогенізатори вимагає попереднього видалення з палива води, так як в гомогенизаторах вона не відділяється. Необхідною умовою є також установка за гомогенізатором фільтра тонкого очищення палива.