Термоусаджувальні трубки. Все про головне (частина 3)
Технологія виробництва термоусаджуваних трубок

Мал. 1. Екструзійний цех
Виробництво термоусаджуваних трубок можна умовно розділити на три етапи: екструзія, зшивання і раздувкой. Виробничий цикл містить також кілька допоміжних технологічних процесів: підготовка полімерної сировини, різання трубок, нанесення клейового шару і упаковка.
Технологія здається простою, але нюанси вимагають від кожного виробника власних ноу-хау. винахідливості і кмітливості з боку технологів та інженерів. Навіть якщо виробники використовують однакову технологію й устаткування, результат все одно виходить різним.
Розглянемо три основних етапи виробництва термоусаджуваних виробів.
1. Екструзія
Слово «екструзія» походить від позднелатинского «extrusio» - «виштовхування» і позначає продавлювання розплаву або суміші матеріалу через формуючий отвір - фільєру. Екструзія неперервна і вимагає безперебійної подачі сировини до філь'єрі, щоб на виході вийшло виріб з круглим поперечним перерізом і потрібним діаметром. У промисловості переробкою полімерів методом екструзії виготовляють погонажні вироби: труби, листи, плівки та оболонки кабелів. Це робиться за допомогою екструдерів (див. Рис. 1).
Перед тим, як потрапити в завантажувальний бункер екструдера і перетворитися в трубку, інгредієнти полімерного матеріалу ретельно змішуються. Крім полімеру основи - поліолефіну, це можуть бути антипірени - подавители горіння, барвники, пластифікатори, спеціальні добавки. Готова суміш завантажується в екструдер, де нагрівається до температури плавлення. Розплав подається під тиском на фільєру, з якої видавлюється у вигляді трубки. Цей процес нагадує видавлювання крему через насадку кондитерського шприца.
Готова трубка відразу потрапляє в ванну з водою для охолодження і фіксації нової форми. Після охолодження трубка проходить через вузол очищення і намотується на котушку. В процесі екструзії важливо контролювати якість продукту на виході, стежити за рівномірністю товщини стінки і дотриманням потрібного діаметра трубки. Продуктивність екструдера залежить від типу що виготовляються трубок: тонкостінні трубки можна виготовляти швидше, а товстостінні виробляються повільно, тому що матеріал довше охолоджується після екструзії.
Особливість виробництва термоусаджуваної трубки за допомогою процесу екструзії полягає в його безперервності. При відключенні екструдера всередині остигає розплав полімеру, і апарат треба чистити. Повне очищення триває довго і може пошкодити обладнання. Тому на підприємствах часто практикують безперервне виробництво, а при відсутності попиту трубку подрібнюють, і матеріал знову надходить в бункер екструдера по замкнутому циклу. Ця технологія підтримує екструдер в стані готовності для початку оперативного виробництва трубок потрібного діаметру. Іноді процес екструзії трубки називають «витягуванням», хоча це і не зовсім вірно, адже матеріал подається під тиском зсередини назовні, але при спостереженні за роботою екструдера створюється враження, що намотується на котушку готова трубка витягується з екструдера, як нитка з пряжі.
2. Модифікація (зшивання)
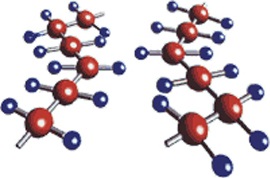
Мал. 2. Ланцюжки молекул поліетилену
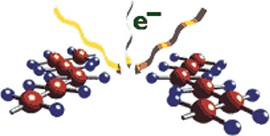
Мал. 3. Відрив атомів водню від полімеру
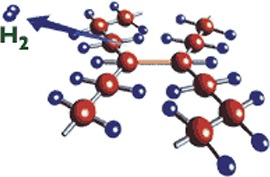
Мал. 4. Об'єднання ланцюжків молекул вуглецю і водню в мережу
Після екструзії виходить заготівля, яку можна застосовувати як ізолюючий кембрік. Але термоусадочної трубка стане тільки після зшивання.
Наведемо трохи теорії. Модифікацією. або зшивкою, називають зміну структури полімерного матеріалу за допомогою фізичного або хімічного впливу на нього ззовні для поліпшення параметрів і додання додаткових властивостей.
В основі процесу зшивання лежить принцип перестроювання внутрішніх зв'язків між молекулами речовини без зміни хімічного складу. Термопластичні матеріали, в нашому випадку поліетилен, складаються з довгих, хаотично з'єднаних вуглеводневих ланцюжків ... -CH2 -CH2 -CH2 - ... (див. Рис. 2).
За допомогою хімічних реакцій або фізичних впливів атоми водню відокремлюються від полімеру (див. Рис. 3).
Завдяки цьому дві сусідні ланцюжки полімеру з'єднуються між собою в місцях, в яких атоми водню відділилися і порушили рівновагу атомів вуглецю. Там залишилися вільними вуглецеві зв'язки, і виникли сильні центри тяжіння, які утворюють міцне з'єднання «вуглець-вуглець» і пов'язують ланцюжка в «мережу» (див. Рис. 4).
Якщо після цього нагріти зшитий поліетилен до температури плавлення його «кристалів», то вийде м'який каучукоподібних еластичний матеріал, а не тягуче-рідка маса, в яку перетворився б поліетилен незшитий.
Полімери в результаті зшивання набувають нову властивість «пам'яті форми». яке і використовується у виробництві термоусаджуваних виробів.
На практиці користуються популярністю два хімічних і один фізичний метод зшивання: пероксидна зшивання, силанового зшивання і радіаційна зшивання. При хімічній зшивці зшивається до 90% всього обробленого обсягу полімеру, але при цьому вона дорожче і небезпечніше для персоналу і навколишнього середовища через отруйності і високої активності застосовуваних хімічних сполук. При радіаційної зшивці досягається менший ефект - зшивається 78% матеріалу, при цьому потрібні дорогі енергетичні установки. Проте, радіаційна зшивання дешевше, більш технологічні і продуктивніше, ніж хімічна, і матеріал при цьому виходить пластичнее і гнучкіше.
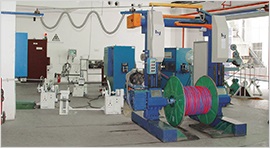
Мал. 5. Цех радіаційної
зшивання полімерів
У виробництві термоусаджуваних трубок найчастіше застосовується радіаційний метод зшивання полімерів, для чого використовуються спеціальні електронні прискорювачі (див. Рис. 5). Електронний прискорювач - великий, складний, високотехнологічний і дорогий комплекс обладнання, що вимагає дотримання заходів безпеки та найму висококваліфікованого персоналу. Не кожна виробляє термонасадкові трубки компанія здатна дозволити собі такі вкладення. Деякі маленькі компанії спеціально укладають контракти на опромінення сировини з великими виробниками - господарями електронних прискорювачів. Наприклад, у компанії WOER у власності відразу чотири електронних прискорювача з Новосибірська.
Більшість виробників термоусаджуваних матеріалів використовують для модифікування гамма-випромінювання. Порівняння характеристик радіаційного модифікування швидкими електронами і гамма-випромінюванням показує, що зі збільшенням щільності матеріалу кількість поглинається їм енергії пучка електронів швидко зменшується. Для гамма-випромінювання цей спад більш пологий. Спосіб модифікування сильно впливає на властивості термоусаджуваних матеріалів. Матеріали, оброблені гамма-випромінюванням. відрізняються більш високим коефіцієнтом усадки, більш низькою температурою усадки і більш високою еластичністю в порівнянні з опроміненням швидкими електронами.
Зшивання виглядає так: після екструзії котушку з трубкою поміщають в опромінюють камеру або розтратив через сфокусований електронний промінь в робочій камері електронного прискорювача. У другому випадку зшивання йде безперервно, що підвищує продуктивність і впливає на глибину зшивання шляхом зміни швидкості проходження трубки через прискорювач.
3. раздувкой
Розширення або раздувкой (по-англійськи «expanding») завершує перетворення зшитих полімерних заготовок в повноцінну термоусаживающихся трубку. Так як сировину, що минув радіаційну модифікацію, вже набуло «пам'ять» первісної форми, тепер можна поперечно розтягнути трубку в 2-3 рази до необхідного збільшеного діаметру. При нагріванні поперечно розширеної трубки вона «згадає» свої статки до розширення і всядеться до початкового розміру.
Принцип пам'яті форми полягає в тому, що зшита трубка має більш впорядковану тривимірну структуру, на зразок кристалічної решітки. Розтягуючи трубку, розігріту до температури, близької до температури плавлення, ми збільшуємо відстань між молекулами, деформуємо і розтягуємо, як гумку, міжмолекулярні зв'язки, але не рвемо їх. Після охолодження трубка як би кристалізується, тримає нову форму, але при нагріванні або поздовжньої деформації прагне повернутися в початкове стислий стан.
Для поперечного розтягування трубки використовують спеціальні верстати - експандери. Принцип дії і конструкція різняться, але всі вони засновані на механічному принципі розтягування. Найбільш часто застосовуються експандери, що використовують різницю тисків стиснутого повітря для розтягування трубки зсередини (роздування) або розтягування вакуумом. Через цю особливість процес розтягування часто називають раздувкой. При такому методі трубка нагрівається, подається в спеціальну камеру, роздувається в ній зразок повітряної кульки, приймає задану камерою форму і інтенсивно охолоджується в новому розмірі.
Для тонкостінних гнучких термоусаджуваних трубок процес раздувкой автоматизований і дозволяє добитися високої продуктивності. Опромінена заготівля змотується з бобіни, пропускається через експандер і, вже роздута, готова термоусадка знову намотується на бобіну.
До сих пір на деяких виробництвах в Китаї зустрічається метод ручної механічної раздувкой товстостінних термоусаджуваних трубок. Трубка поміщається в металеву трубу. Всередину трубки простягається рукав з міцного полімерного або тканого матеріалу, на одному кінці якого знаходиться шланг з клапаном. З цього шлангу в рукав подається стиснене під великим тиском повітря, рукав під тиском роздувається і рівномірно розтягує трубку в ширину по всьому об'єму металевої форми. В результаті виходить ідеально рівна толстостенная термозбіжна трубка. Продуктивність цього методу невисока, але китайці справляються.
Спосіб розширення трубок впливає на поздовжню усадку, величина якої варіюється від 1 до 10%.
Після завершення третього етапу ми отримуємо готовий продукт - термоусаживающихся трубку, яку вже можна застосовувати за призначенням. Але перед поставкою продукції кінцевому споживачеві буває необхідно провести ряд додаткових операцій, таких як різання по встановленому розміру, нанесення клейового шару, нанесення маркування, упаковка. Коротко розповімо про кожну.
маркування
При необхідності на тонкостінні трубки за допомогою спеціального кліше, виконаного у вигляді металевого ролика, можна нанести маркування. Частина цього ролика занурюється в ємність з барвником пігментом. Ролик притискається до трубки і приводиться в рух за рахунок протягування трубки через верстат. При кожному оберті колеса на трубці через рівні проміжки друкується чіткий відбиток. Наноситься інформація може містити назву трубки, технічну маркування, основні технічні характеристики і торгові знаки.
Нанесення клейового шару
При виробництві клейовий трубки після раздувкой на внутрішню поверхню стінок наносять термоплавкий клей. Ця операція виконується по-різному. У деяких компаніях клей наносять вручну - пензликом або спеціальним поршнем (для трубок великого діаметра). У деяких компаній з сучасною виробничою базою, наприклад компанії WOER, нанесення клею відбувається ще на першому етапі, при екструзії трубки. Спеціальний екструдер має головку з подвійною подачею сировини, при цьому трубка і клейовий шар витягуються одночасно. Клей розігрівається до рідкого стану і наноситься в автоматичному режимі тонким шаром на внутрішню поверхню трубки під час її протягування через верстат. Клей рівномірно розподіляється по стінках і застигає, після чого трубка стає жорсткою. Таку трубку важко (а великі діаметри неможливо) згорнути в бухти без зламів, тому клейова трубка, за винятком дуже маленьких діаметрів, поставляється в нарізці.
Різка і упаковка
Термоусаживающихся трубку поставляють в двох видах: в бухтах по 25 ... 200 метрів або мірними відрізками.
Найчастіше трубку нарізають відрізками по 1 метру і упаковують в поліетиленові пакети. Для клейових термоусаджуваних трубок стандартно використовується довжина відрізка 1,22 метра (4 фути). Максимальна довжина відрізка клейовий трубки може становити 1,5 ... 2,0 метра, проте довжина трубки більш 1,22 метра створює серйозні незручності при транспортуванні.
Термоусаживающихся трубку ріжуть на спеціальних машинах для різання, що працюють за принципом гильотин з автоматичною подачею. За даними компанії WOER, тонкостінна трубка нарізається з точністю від ± 1 до ± 5 мм. Нарізка на необхідну клієнтові довжину дозволяє використовувати трубку без відходів, і це вигідно оптовим покупцям.
Властивості клейового шару термоусаджуваних трубок
Клейовий шар більшості клейових термоусаджуваних трубок виготовляють на основі полімеру - етиленвінілацетату (EVA), що відноситься до поліолефінової групі. У Росії цей матеріал часто називають севіленом. Всі модифікації клею на основі етиленвінілацетату плавляться при температурі в діапазоні від +80 до + 95 ° С. У рідко-в'язкому стані EVA прилипає до металів, дереву та інших матеріалів. Після охолодження клей твердне і схоплюється з поверхнею.
Товщина клейового шару залежить від призначення трубки. Тонкий клейовий шар використовується для поліпшення адгезії трубок до поверхні. Товстий шар термоклею ретельно герметизирует порожнечі і нерівності поверхні, при цьому надлишки клею випливають назовні з двох сторін обсаджений трубки.
Коефіцієнт усадки клейових трубок - не менше трьох до одного. Так само, як і при усадки трубки, при стисненні клейового шару зменшується займаний ним всередині трубки обсяг, при цьому кількість клею не змінюється. Отже, клей прагне рівномірно розподілитися по всьому об'єму, знаходячи будь-який вільний простір. При відсутності такого клей випливає, видавлюючи з обох кінців усадженої трубки.
Клей, як і звичайний поліолефін, непогано горить. При виборі термоусаджуваних трубок з придушенням горіння майте на увазі, що через термоплавкого клею самозагасання відбувається повільніше або навіть не відбувається зовсім. Ефект горіння термоклею не говорить про те, що матеріал-основа термоусаджуваної трубки горіння не пригнічує. Щоб тестувати матеріал-основу на горючість, видаліть клейовий шар.