1.1 Функціональна схема виробництва метанолу
Технологічний процес отримання метанолу з оксиду вуглецю і водню включає ряд операцій, обов'язкових для будь-якої технологічної схеми синтезу. Газ попередньо очищається від карбонила заліза, сірчистих сполук, підігрівається до температури початку реакції і надходить в реактор синтезу метанолу. Після виходу із зони каталізу з газів виділяється утворився метанол, що досягається охолодженням суміші, яка потім стискається до тиску синтезу і повертається в процес.
Функціональна схема виробництва метанолу приведена на малюнку 1.1 [1].
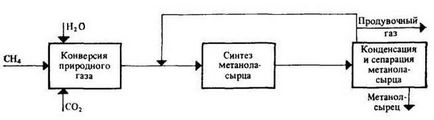
Малюнок 1.1 - Функціональна схема виробництва метанолу
1.2 Фізико-хімічні основи процесу
Синтез метанолу заснований на оборотних реакціях, описуваних рівняннями:
CO + 2H2 CH3 OH; DH = -90.8 кДж
Обидві реакції екзотермічни і протікають зі зменшенням обсягу. З цього випливає, що для досягнення максимальних значень виходу метанолу і ступеня перетворення синтез-газу необхідно проведення процесу при низьких температурах і високому тиску.
Максимально досяжна ступінь перетворення синтез-газу при цьому обмежена умовами рівноваги реакцій отримання метанолу, які вивчені експериментально і теоретично [1]. На підставі отриманих практичних даних можна при наближених розрахунках обмежиться тільки першою реакцією, так як частка оксиду вуглецю (IV) у вихідній суміші незначна.
Для збільшення швидкості реакції необхідно підвищення температури. При цьому, вибираючи оптимальний температурний режим, слід враховувати освіту побічних сполук: метану, вищих спиртів, кислот, альдегідів, кетонів і ефірів [1].
Ці реакції зумовлюють даремний витрата синтез-газу і здорожують очищення метанолу. Застосовуваний для синтезу метанолу каталізатор повинен мати високу селективність, т. Е. Максимально прискорювати освіту метанолу при одночасному придушенні побічних реакцій.
1.3 Каталізатори синтезу метанолу
Застосовуваний для синтезу метанолу каталізатор повинен мати високу селективність, т. Е. Максимально прискорювати освіту метанолу при одночасному придушенні побічних реакцій. Для синтезу метанолу запропоновано багато каталізаторів. Кращими виявилися каталізатори, основними компонентами яких є оксид цинку або мідь (застосовується при тиску 5,5 МПа) [1].
На перших великотоннажних установках процес здійснювався при тиску близько 30 МПа на цинк-хромовому каталізаторі. У наступні роки набули широкого поширення схеми синтезу при зниженому тиску на низькотемпературних медьсодержащих каталізаторах.
Каталізатори синтезу метанолу дуже чутливі до каталітичним отрут, тому першою стадією процесу є очищення газу від сірчистих сполук. Сірчисті з'єднання отруюють цинк-хромові каталізатори можна зупинити, а медьсодержащие каталізатори - є незворотнім.
Необхідна також ретельне очищення газу від карбонила заліза, який утворюється в результаті взаємодії оксиду вуглецю з залізом апаратури. На каталізаторі карбоніл заліза розкладається з виділенням елементного заліза, що сприяє утворенню метану.
1.4 Режимні параметри процесу синтезу метанолу
Залежність виходу метанолу від температури не лінійна і має виражений максимум. Крива залежності кількості утворився метанолу від температури проходить через екстремум при всіх складах газу, причому максимальний вихід метанолу спостерігається при 255-270 ° С.
Інтервал оптимальних температур, відповідних найбільшому виходу продукту, визначається активністю каталізатора, об'ємною швидкістю газової суміші і тиском. Процеси низького тиску (5-10 МПа) на медьсодержащих каталізаторах здійснюють при температурах 220-280 ° С. Для цинк-хромового каталізатора характерні більш високі тиску (20-30 МПа) і температури (350-400 ° С).
Максимальний тиск, що застосовується в промислових синтезах, становить 40 МПа; вище цього тиску прискорюються побічні реакції і, крім того, збільшення витрат на компресію газу погіршує економічні показники процесу. У синтезах низького тиску підвищення тиску обмежена термічною стабільністю мідних каталізаторів.
Із зростанням об'ємної швидкості газу вихід метанолу падає. Це справедливо для синтезу як при високому, так і при низькому тиску. Така закономірність заснована на тому, що зі збільшенням об'ємної швидкості зменшується час контакту газу з каталізатором і, отже, концентрація метанолу в газі, що виходить з реактора [1].
Склад газової суміші істотно впливає на ступінь перетворення сировини і продуктивність каталізатора. У промислових умовах завжди працюють з деяким надлишком водню; максимальна продуктивність спостерігається при молярному відношенні Н2: СО = 4, на практиці підтримують відношення 2,15-2,25.
1.5 Технологічні схеми виробництва метанолу
Технологічний процес отримання метанолу з оксиду вуглецю і водню включає ряд операцій, обов'язкових для будь-якої технологічної схеми синтезу. Газ попередньо очищається від карбонила заліза, сірчистих сполук, підігрівається до температури початку реакції і надходить в реактор синтезу метанолу. Після виходу із зони каталізу з газів виділяється утворився метанол, що досягається охолодженням суміші, яка потім стискається до тиску синтезу і повертається в процес.
Технологічні схеми розрізняються апаратурним оформленням головним чином стадії синтезу, що включає основний апарат колону синтезу і теплообмінник [1].
На малюнку 1.2 представлена схема агрегату синтезу метанолу під тиском 5.5 МПа
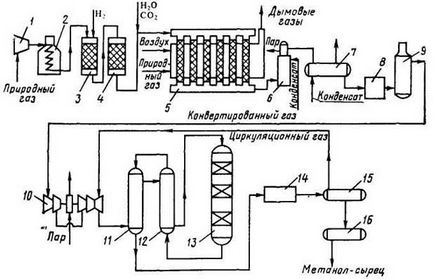
Малюнок 1.2 - Схема виробництва метанолу при тиску 5 МПа
1, 10 - турбокомпресори; 2 - підігрівач природного газу; 3 - реактор гідрування сірчистих сполук; 4 - адсорбер; 5 - трубчастий конвертор; 6 - котел-утилізатор; 7, 11, 12 - теплообмінники; 8, 14 - холодильники (АВО); 9, 15 - сепаратори; 13 - колона синтезу; 16 - збірник
Природний газ стискається турбокомпресором 1 до тиску 3 МПа, підігрівається в підігрівач 2 за рахунок спалювання в міжтрубномупросторі природного газу і направляється на сіркоочистки в апарати 3 і 4, де послідовно здійснюється каталітичне гідрування органічних сполук сірки і поглинання утворюється сірководню адсорбентом на основі оксиду цинку. Після цього газ змішується з водяною парою і діоксидом вуглецю в співвідношенні СН4. Н2 О. СО2 = 1. 3,3. 0,24. Суміш направляють в трубчастий конвертор 5, де на нікелевому каталізаторі відбувається пароуглекіслотная конверсія при 850-870 ° С. Теплоту, необхідну для конверсії, отримують в результаті спалювання природного газу в спеціальних пальниках.
Конвертований газ надходить в котел-утилізатор 6, де охолоджується до 280-290 ° С. Потім теплоту газу використовують в теплообміннику 7 для підігріву живильної води, що спрямовується в котел-утилізатор. Пройшовши повітряний холодильник 8 і сепаратор 9, газ охолоджується до 35-40 ° С.
Охолоджений конвертований газ стискають до 5 МПа в компресорі 10, змішують з циркуляційним газом і подають в теплообмінники 11, 12, де він нагрівається до 220-230 ° С.
Нагріта газова суміш надходить в колону синтезу 13, температурний режим в якій регулюють за допомогою холодних байпасів. Теплоту реакційної суміші використовують в теплообмінниках 11, 12 для підігріву надходить в колону газу.
Далі газова суміш охолоджується в холодильнику-конденсаторі 14, сконденсувалася метанол-сирець відділяється в сепараторі 15 і надходить до збірки 16. Циркуляційний газ повертають на синтез, продувні і танкові гази передають на спалювання в трубчасту піч.
Внаслідок зниження температури синтезу при низькому тиску процес здійснюється в умовах, близьких до рівноваги, що дозволяє збільшити продуктивність агрегату.
Приймаємо для проектування технологічну схему синтезу метанолу при низькому тиску (5,5 МПа).