Вибір литого обладнання є однією з поширених завдань, що вирішуються при проектуванні технологічних процесів виготовлення виробів з термопластів. Вихідними даними для вирішення цього завдання служать відомості по кількості і асортименту виробів, що випускаються або намічаються до випуску. Визначається також перелік видів (типорозмірів) ливарних машин, на базі яких планується проводити технічне оснащення виробництва. Для кожного виробу типорозмір литтєвий машини вибирається таким чином, щоб при цьому гарантувалося досягнення необхідної якості виробів і забезпечувалися найкращі техніко-економічні показники виробництва.
Однак крім основних параметрів, що визначають типорозмір (зусилля змикання форм, обсяг вприскування і Пластікаціонная продуктивність), фахівцю доводиться вирішувати цілий ряд інших завдань, пов'язаних з технологією лиття, особливістю конструкції майбутнього виробу, питаннями економіки і т.д. Причому рішення можуть виявитися принципово різними, коли мова йде про придбання нового обладнання або про використання вільних потужностей ливарних машин, вже наявних на даному виробництві.
1. Класифікація ливарних машин
Ливарні машини належать до найбільш затребуваних видів обладнання для переробки пластмас. Тому природно, що для виробництва величезної номенклатури ливарних виробів машинобудівними фірмами випускається дуже широка гама машин різної конструкції і призначення. Ця обставина сприяло тому, що для упорядкування цього розмаїття було запропоновано багато класифікаційних ознак.
По виду переробляється полімеру машини діляться на термопластавтомати (для переробки термопластичних матеріалів), реактопластавтомати (для переробки термореактивних матеріалів), машини для лиття виробів з гумових сумішей. До завдань даного навчального посібника входить опис методики вибору термопластавтоматів.
За призначенням ливарні машини поділяють на універсальні, спеціальні, лабораторні та машини для Мікроліти.
Універсальні машини призначаються для виробництва найширшого асортименту виробів, їх конструкція передбачає зручність і швидкість заміни ливарних форм, а система управління дозволяє міняти в широких межах технологічні параметри лиття. Схема одного з можливих варіантів конструкції універсальної машини представлена на рис. 1. Основні компоненти литтєвий машини - вузол пластикации і вприскування, вузол змикання форм і компоненти приводу, включаючи систему електрокерування.
Спеціальні машини створюються для виробництва вузької номенклатури близьких по конструкції виробів і, як правило, включають в себе додаткові вузли, не властиві універсальним машинам. Досить часто
ці машини призначаються для виробництва тільки одного виду вироби. У ряді випадків спеціальні машини є складовою частиною складних автоматизованих технологічних ліній. Іноді вони використовуються для здійснення «нестандартних» технологій лиття під тиском (табл. 1).
Мал. 1 Схема одного з можливих варіантів конструкції універсальної машини
Класифікація спеціальних технологій лиття під тиском
Машини звичайні лабораторні зазвичай не великі за своїми розмірами, служать, як правило, для відпрацювання технології лиття виробів з нових марок полімерних матеріалів, їх система управління дозволяє міняти в широких межах технологічні параметри лиття. Вони пристосовані для швидкої заміни формуючого інструмента та, в порівнянні з виробничими машинами, оснащені додатковими датчиками, що дозволяють відслідковувати всі етапи технологічного процесу лиття.
За обсягом упорскування машини підрозділяються в залежності від максимального обсягу палива, що впорскується за один цикл матеріалу. Досить довгий час цей класифікаційний ознака вважався основним, проте, останнім часом, він по ряду причин відійшов на другий план. Незважаючи на це, саме обсяг вприскування поряд із зусиллям змикання форм визначає в кінцевому підсумку габарити машини і можливості виробництва на ній тих чи інших виробів.
В основу створення ряду машин для виробництва виробів різних габаритів більшість машинобудівних фірм в даний час закладають номінальне зусилля змикання форм, яке також вважається одним з класифікаційних ознак.
За кількістю квітів одного полімеру або кількості різних полімерів, представлених в конструкції відливаються виробів, машини підрозділяються на однокомпонентні, двокомпонентні і багатокомпонентні. В даний час відомі машини для лиття виробів з восьми компонентів.
По взаємному розташуванню вузлів, що виконують однакові функції в процесі роботи, машини підрозділяють на машини горизонтальні (рис.2, а), кутові машини з горизонтальною компонуванням (рис. 2, б, вид зверху), кутові машини з вертикальним (рис. 2 , в) і машини вертикальні (рис. 2, г).
Компонування машин визначається багатьма факторами: вимогами технології, конструкцією відливаються виробів, ступенем автоматизації і роботизації процесу, міркуваннями економії виробничих площ і т. Д.
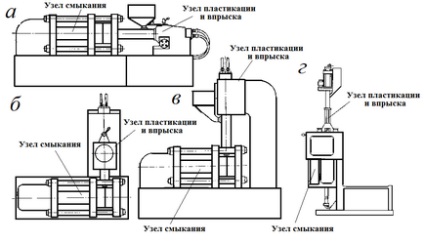
Мал. 2 Литтєві машини з різним взаємним розташуванням вузлів
Варіанти компоновки, наведені на рис. 2, характерні для машин, призначених для однокомпонентного лиття. Машини для багатокомпонентного лиття являють собою досить складні поєднання наведених вище прикладів.
Найбільш поширені на виробництві машини горизонтального типу, проте поряд з ними досить широко в промисловості використовуються як вертикальні ливарні машини, так і кутові машини з горизонтальною або вертикальним вузлів під прямим кутом.
Переваги вертикальних ливарних машин:
вони займають невелику виробничу площу; легко вбудовуються в технологічний ланцюжок з іншим обладнанням;
зручні при литті в напівстаціонарних форми, горизонтальна площина роз'єму яких значно полегшує установку знімних оформляють деталей (різьбових знаків і кілець, різних вставок, арматури та інших елементів).
Залежно від можливостей встановленого на них формуючого інструмента та використовуваної робототехніки вертикальні ливарні машини можуть працювати в ручному або напівавтоматичному режимі. В автоматичному режимі вони працюють порівняно рідко, оскільки потрібні досить складні робототехнічні пристрої для видалення з них готових виробів.
Основним недоліком вертикальних ливарних машин є їх обмеження по потужності, зі зростанням якої збільшується і висота машин, що ускладнює їх обслуговування і вимагає великої висоти виробничих приміщень.
Кутова компоновка машин використовується деякими фірмами-виробниками при створенні машин для лиття великогабаритних або складно армованих виробів, так як вони відрізняються зручністю в обслуговуванні, особливо при литті великих виробів з утрудненим витягом з форми. Широке поширення набуло створення на базі кутових машин установок для багатоколірного або багатокомпонентного лиття (рис.3).
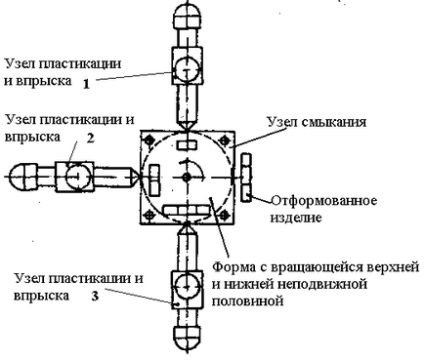
Мал. 3. Розташування вузлів пластикации і уприскування на кутовий литтєвий машині для трьохпозиційного лиття триколірних деталей
Машина, показана на рис. 3, має центральний вертикальний вузол змикання, навколо якого в горизонтальній площині розташовані вузли пластикации і уприскування. Розплав зазвичай впорскується по лінії роз'єму. Одна півформа, зазвичай верхня половина, може обертатися навколо вертикальної осі (кут повороту 180 °, 120 ° або 90 °) і переміщати відформоване виріб з позиції 1 на позицію 2, а потім на позицію 3. На кожній з цих позицій в вільну формующую порожнину , утворену після закриття і повторного змикання, вводиться новий матеріал.
До переваг конструкції даних ливарних машин відносяться, по-перше, виробництво за один робочий цикл різнокольорових виробів в литтєвий формі заданої (1, 2, 3 і т.д.) гнёздності. Ці переваги забезпечують підвищення продуктивності праці, завдяки виключенню збірки окремо формованих різнокольорових деталей. По-друге, малий рівень залишкових напружень і дуже низький відсоток браку багатобарвних виробів внаслідок «гарячого» з'єднання один з одним їх окремих кольорових елементів.
2. Особливості та призначення вузлів пластикации різного типу
Відповідно до методу пластикации матеріалу ливарні машини можна класифікувати за такими ознаками:
за конструктивним оформленням (одно- і двоциліндрові);
по числу шнеків в одному циліндрі (одно- і двухшнековие);
по конструктивно-технологічному (машини без попередньої пластикации і з попередньої пластикацией).
Найбільш компактними, технологічними і забезпечують можливість регулювання основних параметрів лиття в широких інтервалах є одноциліндрові конструкції шнекового типу (рис. 1). У таких конструкціях при пластикации шнек обертається, а при інжекції робить поступальний рух.
Одноциліндровий конструкцію одношнекового типу застосовують для лиття широкого кола виробів, в тому числі для виготовлення товстостінних виробів. Двоциліндрові конструкції одношнекового типу дозволяють отримувати двоколірні товстостінні вироби.
Одноциліндрові конструкції двухшнековие типу використовують для переробки порошкоподібних полімерів.
У машинах без попередньої пластикации шнек поряд із забезпеченням пластикации розплаву виконує роль поршня при уприскуванні розплаву в форму; при цьому час пластикации поєднане частково з часом уприскування.
У машинах з попередньої пластикацией полімер пластикується в Пластікаціонная циліндрі, після чого впорскується в форму при переміщенні поршня (шнека) в інжекційних циліндрі, т. Е. Стадії пластикации і уприскування розділені.
В даний час застосовують двоциліндрові конструкції з Пластікаціонная циліндром шнекового типу, наприклад, для лиття преформ (рис.4).
У цих конструкціях шнек в Пластікаціонная циліндрі обертається, забезпечуючи пластикации полімеру, після закінчення якої пластицирован полімер переміщається через клапан перемикання в інжекційні циліндр.
Найбільш важливий компонент вузла пластикации - шнек. Шнек відповідає за транспортування, розігрів, змішування і уприскування полімерного матеріалу в форму, а в деяких випадках і за видалення газів з циліндра шнека. Зазвичай використовуються трьохзонний шнеки (рис. 5) з відношенням довжини шнека до діаметру (L / D) приблизно 20: 1 ± 10%. При застосуванні коротких шнеків якість розплаву погіршується. Довші шнеки з співвідношенням L / D 24: 1 і більше можуть призводити до деструкції ряду полімерних матеріалів внаслідок збільшення часу їх перебування в шнеку.
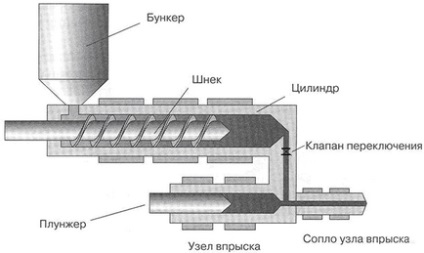
Рис.4. Двоциліндрова конструкція поршневого инжекционного вузла з
Пластікаціонная циліндром шнекового типу
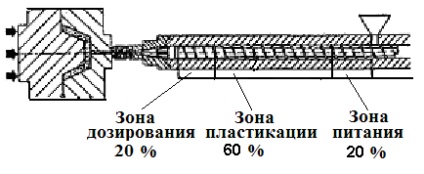
Мал. 5. трьохзонний шнек для переробки термопластів
Основними властивостями полімерів, що визначають профіль шнека, є характер переходу в в'язкотекучий стан (визначає співвідношення довжин зон харчування і пластикации), термостабільність і чутливість матеріалу до зсувними напруженням (визначають межвиткового обсяг і ступінь стиснення). За цими ознаками полімери можна розділити на три групи. Для кожної з груп застосовують спеціальний шнек.