Проектування опор валів на підшипниках ковзання
Переваги перед підшипниками кочення:
- надійність роботи при ударних і вібраційних навантаженнях в умовах запиленості та широкому інтервалі температур;
- працездатність при високій частоті обертання валу;
- здатність підшипників, виконаних з певних матеріалів, працювати без змащення;
\ Несуча здатність підшипника забезпечує застосування мастильного матеріалу - рідкого, газоподібного, пластичного або створення магнітного поля. Залежно від напрямку сприйманого навантаження підшипники поділяють:
Надійно працюють у високошвидкісних приводах
Здатні сприймати значні ударні і вібраційні навантаження через великих робочих поверхонь
Мають порівняно малі радіальні розміри
Роз'ємні підшитий. Допускають установку на шиях колінчастих валів, при ремонті не вимагають демонтажу муфт, шківів і т.д.
Для тихохідних машин мають просту конструкцію.
Високі вимоги до наявності мастильного матеріалу, можливий перегрів.
Великі осьові розміри
Втрати на тертя при пуску і при недосконалою мастилі.
Велика витрата мастильного матеріалу, необхідність очищення і охолодження.
Режим роботи підшипника залежить від величини і характеру навантаження, швидкості ковзання, типу мастила і її фізико-хімічних властивостей, матеріалів поверхні тертя і їх стану. Ці фактори впливають на працездатність, довговічність і надійність підшипника ковзання. Найважливіша характеристика - величина втрат на тертя, які залежать від режиму його роботи. Найважливішим властивістю масел є в'язкість, яка знижується зі збільшенням температури.
Матеріали підшипників ковзання.
Матеріали вибирають з урахуванням роботи в парі зі сталевими шийками вала, які як правило гартують. Пред'являються вимоги: низький коефіцієнт тертя в парі зі сталлю, бути зносостійкими, володіти високим опором втоми. Працездатність підшипника ковзання залежить від твердості шийок валів, тому їх, як правило, гартують.
До підшипниковий матеріалом представляють комплексні вимоги, що відповідають основним критеріям працездатності підшипників ковзання. Вони повинні мати низький коефіцієнт тертя в парі зі сталевою шийкою вала, бути зносостійкими і володіти високим опором втоми.
Першим критерієм задовольняють антифрикційні металеві, металокерамічні і деякі не металеві матеріали.
До металевих матеріалів, найбільш поширеним в машинобудуванні, відносять: антифрикційний чавун, бронзу (олов'янистими і безоловяністую) і цинкові сплави.
Антіфрікационним чавун. Застосовують в тихохідних, помірно навантажених підшипниках з постійною змазкою. Допустимі питомі тиску [р] на робочу поверхню підшипника залежать від окружної швидкості шийки вала (швидкості ковзання) і марки чавуну (АСЧ-1, АСЧ-2, АСЧ-3, АЧК-2) .Для забезпечення зносостійкості шийок вала необхідно вибирати марку чавуну для підшипника так, щоб його твердість була нижче на 20 ... 40НВ в порівнянні з матеріалом цапф.
- Антифрикційний чавун - застосовують в тихохідних, умененно навантажених підшипниках з постійною змазкою. Допустиме питомий тиск на робочу поверхню підшипника залежить від окружної швидкості шийки вала (швидкості ковзання) і марки чавуну. Марку чавуну вибирають так, щоб його твердість НВ була на 20 ... 40НВ нижче, ніж у цапф.
Бронзи. Кращими антифрикційними властивостями характеризуються оловяністие, особливо олов'янистими-фосфористі (БрО10Ф1) бронзи. Їх застосовують для виготовлення вкладишів опор, несучих спокійну навантаження при високій швидкості ковзання (але вони мають високу вартість і по механічної міцності поступаються деяким безоловяністим бронзам, особливо алюмінієвим і свинцевим).
Алюмінієві бронзи. містять залізо мають високу міцність і зносостійкість, але можуть викликати підвищений знос шийки вала, якщо твердість її не вище твердості вкладиша.
Свинцюваті бронзи мають велику ударну в'язкість, вкладиші з них витримують значні знакозмінні і ударні навантаження.
-Бронзи - кращими антифрикційними властивостями володіють оловяністие бронзи і особливо олов'янистими-фосфористі (БрО10Ф1) Застосовується для виробництва вкладишів опор, несучих спокійну навантаження при високій швидкості ковзання, але вони мають високу вартість і по міцності поступаються безоловяністим бронзам (алюмінієві, свинцеві).
Алюмінієві бронзи, що містять залізо - висока міцність, зносостійкість, при твердості шийки вала вище твердості вкладиша.
Свинцюваті бронзи - мають високу ударну в'язкість, витримують значні знакозмінні навантаження.
Підшипники ковзання машин, що працюють з постійним навантаженням.
Підшипники ковзання редукторів, транспортерів, відцентрових насосів
Підшипники ковзання машин, що працюють із змінною і ударної
Безолов'яні алюмінієві сплави типу АСМ. Мають відмінні антифрикційні властивості, але при високих швидкостях ковзання недостатнє опір задиру, чутливі до забруднення масла, мають підвищений коефіцієнт лінійного розширення.
Алюмінієво-оловяністие і цинкові сплави: А09-2, А09-2Б (лиття, біметал); А09-1, А020-1 (прокат, біметал) з підвищеним опором втоми. Сплави забезпечують оптимальну структури і здатні в режимах масляного голодування утворювати на поверхні шийок валу захисну плівку з олова.
Алюмінієві-оловяністие (А09-2, А09-2Б лиття, біметал іА09-2, А020-1 прокат, біметал) з підвищеним опором втоми - забезпечують оптимальну структуру і здатні при масляному голодуванні утворювати захисну плівку з олова
ЦАМ10-5 (10% Al, 5% Cu, остальноеZn), ЦАМ9-1,5 - хороші антифрикційні властивості, висока зносостійкість, недефіцитним вихідних матеріалів, простота виготовлення. Застосовують замість бабітів і бронз.ЦАМ9-1,6 - висока зносостійкість, виготовляють біметалічні вкладиші.
Цинкові сплави - (ЦАМ10-5, ЦАМ9-1,5) - антіфрікационним властивості, висока зносостійкість, недефіцитних вихідні матеріали (застосовують замість бабітів і бронз, роблять біметалічні вкладиші).
Металокерамічні матеріали. Задовільно працюють при поганій мастилі. Мають пористу структури з об'ємом пір 15 ... 35% (вакуумна просочення гарячим маслом). Железографітовие вкладиші, містять до 3% графіту (інше залізо), встановлюють на тихохідних валах в важко доступних для змащення місцях (самозмащувальних підшипників, можуть тривалий час працювати отримуючи масло з пор)
Режими роботи при спокійній навантаженні і 20 ... 25% пористості
Ці підшипники забезпечують низький коефіцієнт тертя (0,04 ... 0,05), зберігають свої антифрикційні властивості в широкому діапазоні температур (до 1000 0 С), характеризуються високою теплопровідністю і корозійну стійкість.
- металлофторопласт - допускають великі питомі тиску до 350МПа; широкий інтервал температур від -200 0 С до +280 0 С, але при температурі понад 120 0 С здатність навантаження знижується, а при 280) З досягає половини початкової величини.
- текстоліт - працюють при температурі не вище 80 0 С;
- поліаміди - малий коефіцієнт тертя (0,1 ... 0,15), стійкість до стирання
- капрон - застосовують де потрібно низький коефіцієнт тертя (0,1 ... 0,15) .Робоча температура не більше 120 0 С.
До недоліків пластмасових підшипників відносимо: розбухання у воді, мала теплопровідність, велика пружна деформація.
Застосовують при експлуатації в курній середовищі; ефективно працюють в опорах зі зворотно-поступальним рухом.
2. Дерев'яні слоістиепластікі мають хорошу зносостійкість. Як мастила використовують рідкі мінеральні масла, воду, емульсію, пластичні мастильні матеріали.
3. Дерев'яні підшипники виготовляють з пресованих брусків берези, бука, дуба з с просоченням пластичними смолами. Припускають невеликі питомі навантаження (до 10 МПа) при v<1м/с.
4. Гума застосовують для облицювання методом гарячої вулканізації робочих поверхонь вкладишів підшипників водяних насосів і машин працюють з водяною мастилом
Розрахунок підшипників ковзання
Для забезпечення довговічності роботи підшипників виконують розрахунок:
- по допустимому питомому тиску, що забезпечує зносостійкість підшипників
- за твором питомої тиску в підшипнику на швидкість ковзання, що характеризує нагрів (за середнім умовному тиску р оцінюється зносостійкість): р = Fr / ld≤ [p]
Робота сил тертя перетворюється в тепло (по рvоценівают теплостійкість): pv≤ [pv]
де Fr - радіальне навантаження на підшипник, Н; lіd- довжина підшипника і діаметр шийки вала, мм; v- швидкість ковзання, м / с. Значення [p] і [pv] залежить від матеріалу вкладиша: для антифрикційних чавунів
[P] = 9МПа, [pv] = 1,8МПа м / с; для бронзи [p] = 10МПа, [pv] = 10МПа м / с; для баббита [p] = 20МПа, [pv] = 75 МПа м / с.
Швидкість ковзання (м / с)
де n- частота обертання валу, хв -1.
Розрахунок виконують як перевірки, так як діаметр шийки вала знаходять при розрахунку вала, а довжину підшипника приймають.
Інтенсивний знос, перегрів і заїдання підшипників обмежує показник [pv] - таблиці.
Довжину підшипника можна визначити заздалегідь задавшись матеріалом (таблиця). Отриману довжину порівнюємо з рекомендованою. Ставлення l / d = 0,5 ... 1,5. З увеліченіемdотношеніеl / d- зменшується: чим довше шийка вала, тим більше нерівномірність розподілу навантаження по її довжині і вище місцевий знос втулки або вкладиша на його краях. Підшипники Сl / d> 1 можна приймати для збільшення жорсткості валів.
Допустимі режими роботи для підшипникових матеріалів:
Визначити параметри підшипника ковзання для вала мотовила комбайна (Дон-1500) при следуюший вихідних даних d = 60мм; частота обертання мотовилі 49 хв -1; зусилля; чинне на цапфу від ланцюгової передачі приводу мотовила, состовляетFr = 4010Н.
1.Из додатки 36 приймаємо стандартні розміри втулки підшипника ковзання. Для d = 60 ммL = 60 мм.
2. Визначаємо питомий тиск на підшипник ковзання
3. Розраховуємо швидкість швидкість цапфи вала по робочій поверхні підшипника ковзання
4. Визначаємо твір pv,
1.Режіми роботи підшипників ковзання
При виборі підшипників ковзання необхідно враховувати їх переваги перед підшипниками кочення: надійність роботи при ударних і вібраційних навантаженнях в умовах запиленості та в широкому діапазоні температур; працездатність при високій частоті обертання; здатність деяких матеріалів підшипників працювати без змащення; безшумність роботи.
Режим роботи підшипників залежить від величини і характеру навантаження, швидкості ковзання, типу мастила і її фізико-хімічних властивостей, матеріалів поверхонь тертя і їх стану і ... Найважливіша характеристика підшипників ковзання - величина втрат на тертя, яка залежить від режиму його роботи. При дуже малій швидкості ковзання (менш 0,01 м / с) і відсутності мастила - маємо сухе тертя. Опір обертанню вала в цьому випадку визначає лише коефіцієнт тертя, що труться. При наявності змащення робочі поверхні вала і підшипника покриваються найтоншим адсорбованим масляним шаром (до 0,1мкм), званим граничним. Він стійкий до руйнування і великих навантажень. Але в місцях зосередженого тиску, де висота мікронерівності максимальна відбувається схоплювання відрив мікрочастинок матеріалів, що призводить до зносу поверхонь, але меншому ніж при сухому терті. При збільшенні швидкості ковзання наявності мастила вал обертаючись захоплює мастильний матеріал в мікронерівності і створюється гідродинамічна підйомна сила. зменшує радіальне навантаження на поверхню підшипника. Таке тертя називається напіврідинних. Коефіцієнт напіврідинного тертя для антифрикційних матеріалів 0,008 ... 0,1.
Збільшення швидкості ковзання призводить до зростання гідродинамічної підйомної сили і робочі поверхні підшипника і вала не стикаються одна з одною. Вид тертя називається рідинним і забезпечує високу зносостійкість, опір заїдання валу і високий ККД підшипника.
Розрахунок підшипника при рідинної мастилі.
Радіальна сила сприймається підшипником: Fr =
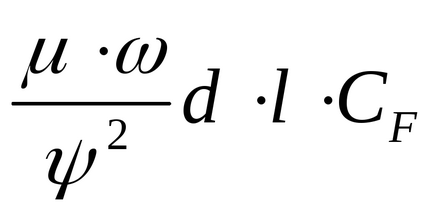
де μ - динамічна в'язкість масла; ω - кутова частота обертання валу;
ψ = (D d) / d - відносний зазор: D - діаметр отвору вкладиша; CF - безрозмірний коефіцієнт навантаження (число Зоммерфельда), вибирається за довідником в залежності від дуги охоплення, відносної довжини підшипника і відносного ексцентриситету (е - ексцентриситет);
При відомої радіальної силі, визначаємо коефіцієнт навантаженості:
CF = p · ψ 2 / μ · ω. де р = Fr / d · l За таблицями знаходимо χ, обчислюємо мінімальну товщину масляного шару hmin = 0,5ψ · d (1-χ) і порівнюємо її з необхідною за умови існування рідинного змащення hmin = 2 (Rz1 + Rz2)
де Rz1. Rz2 - висота профілів микронеровностей поверхонь цапфи і вкладиша.
З умови граничної і напіврідинних мастила визначити силу тертя і моменти сил тертя расчетниім шляхом не вдається. В умовах рідинного змащення сила тертя: FTp =
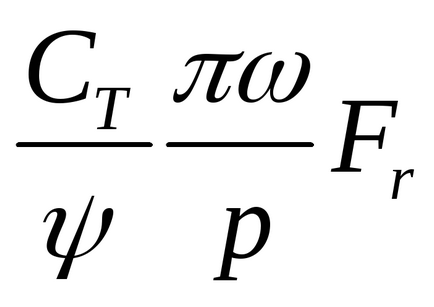
де СТ - безрозмірний коефіцієнт опору обертанню, який обчислюється наближено: CT =
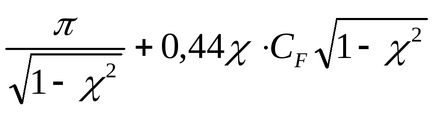
Використовуючи силу тертя визначають тепловиділення і ККД.
Тепловий розрахунок підшипників
Температуру підшипника визначаємо з рівняння теплового балансу між тепло освітою і тепловіддачею при сталим тепловому режимі. Потужність теплоутворення в підшипнику: W1 = Fr · ψ · υ · CT / CF
Тепловідведення відбувається через корпус, вал і мастильний матеріал. Потужність, W2 відведена через корпус підшипника: W2 = KT A (tk - t0).
де KT = 15 ... 20 Вт / (м 2 0 С) - коефіцієнт тепловіддачі; А - площа поверхні корпусу підшипника, що контактує з повітрям; tk і t0 - температура корпусу і навколишнього середовища. Тепло відведення через вал враховують збільшенням площі поверхні корпусу на величину (5 ... 8) d 2
Потужність тепло відводу через мастильний матеріал: W3 = c · V · ρ (tвих - tвх)
де с - питома теплоємність масла; V- об'ємний витрата масла; ρ - щільність масла; tвих і tвх - температура масла на виході і вході в підшипник.
З рівняння теплового балансу: W1 = W2 + W3
визначаємо температуру масла. яка при тривалій роботі не повинна перевищувати 80 0 С.