У вітчизняній промисловості ручні різаки інжекторного типу для кисневого різання знаходять поки найширше застосування, незважаючи на активне просування виробниками і продавцями протягом останніх 10-ти років більш ефективних і безпечних ризиків з внутрісопловим змішанням газів.
Домінуюче становище ризиків інжекторного типу обумовлено цілим рядом умов:
в Радянському Союзі в масовому порядку проводилися тільки інжекторні різаки, що дозволило довести технологію їх виготовлення до дуже високого рівня, яка взята за основу всіма підприємствами, що виробляють даний вид продукції на території РФ та інших країн СНД в даний час;
собівартість виготовлення інжекторних різаків практично у всіх виробників цього виду газопламенного обладнання невисока і відрізняється незначно, що вкрай важливо в конкурентній боротьбі;
споживачі, протягом десятків років експлуатували інжекторні різаки, продовжують їх купувати, з тією лише різницею, що в даний час изза появи нових підприємств, їм доводиться вибирати, продукцію якого виробника придбати.
Незважаючи на те, що конструкція інжекторних різаків відпрацьована, випускаються вироби, які на догоду зниження вартості втрачають ряд конструктивних і експлуатаційних властивостей, знижується їх надійність, працездатність і безпеку. Більш того, останнім часом з'явилися неякісні підробки ризиків і запасних частин до них, виготовлені в Китаї. Така ситуація змушує споживачів більш серйозно підходити до вибору придбаної продукції.
У ТОВ «СКТБ АВТОГЕНТЕХМАШ», як до розробника газопламенного обладнання, надходили і продовжують надходити запити дати об'єктивну оцінку пропонованим на російському ринку інжекторним різаків. Для цього потрібне проведення випробувань ризиків, які використовуються російськими споживачами. Для об'єктивності ТОВ «СКТБ АВТОГЕНТЕХМАШ» запропонувало провідним виробникам представити зразки для проведення випробувань, мета яких полягає в наступному:
- оцінка продукції, представленої на російському ринку, на відповідність чинному в РФ ГОСТ 5191;
- оцінка продукції на відповідність заявленим паспортним характеристикам;
- організація взаємодії розробників і виробників автогенної техніки в області розробки нової та вдосконалення випускається техніки.
Більшість постачальників ризиків зацікавилося пропозицією про проведення випробувань, але поки не представлені зразки від ряду провідних виробників і робота не закінчена. Щоб допомогти споживачам вибрати з запропонованої продукції ту, яка відповідає їх вимогам, а також забезпечить високу надійність і кращу якість роботи, складемо опис оптимальної конструкції і перелік вимог, яким повинні відповідати інжекторні різаки.
Особливості конструкції інжекторних різаків
Інжекторними називаються різаки, в яких горючий газ надходить в змішувальну камеру внаслідок інжектується дії кисневої струменя, що витікає з сопла інжектора з критичною швидкістю. На рис. 1 представлена оптимальна конструкція інжекторного вузла, що забезпечує надійну і безпечну роботу різака. Все газодинамічні характеристики інжекторного вузла у взаємодії з мундштуком давно вивчені, розраховані і підтверджені дослідними даними. Тому завдання виробників сьогодні, незалежно від конструктивних особливостей, витримати відомі співвідношення між нижчезазначених конструктивними елементами ризиків.
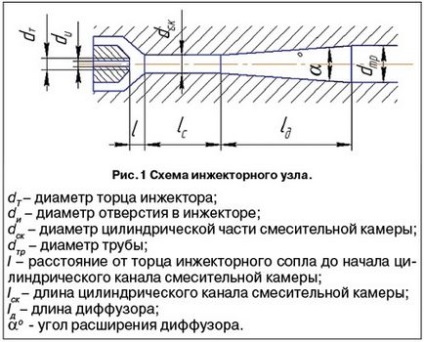
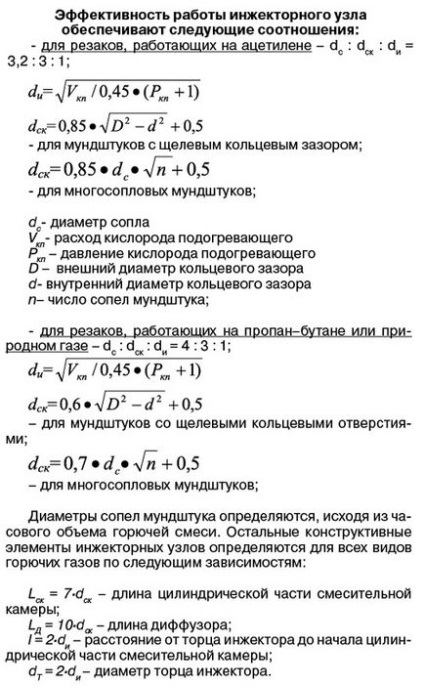
На сьогодні є точно встановлені, підтверджені дослідженнями ВНІІАвтогенмаша, розміри для прохідних перетинів вихідних каналів інжекторів і циліндричних каналів змішувальних камер для горючих сумішей ацетилену з киснем і пропанбутану (природного газу, метану) з киснем, що забезпечують надійну, економічну і безпечну роботу інжекторних різаків.
Для горючої суміші кисню і ацетилену:
Для горючої суміші кисню і пропанбутану (природного газу, метану):
dи = 0,95 мм; Dск = 2,8 мм.
Наведені формули дозволять нам більш детально описати роботу інжекторного вузла і мундштука різака.
Підігріває кисень надходить в інжектор, звідки випливає з великою швидкістю і потрапляє в змішувальну камеру, захоплюючи за собою горючий газ. Сила інжекції зменшується по довжині струменя, тобто подсасиваніе горючого газу на початку змішувальної камери йде більш інтенсивно і плавно зменшується в напрямку закінчення. Величина розрідження в каналі горючого газу тісно пов'язана з точністю виготовлення газових каналів інжекторного вузла. Дуже важливо, щоб вісь сопла інжектора збігалася з віссю циліндричного каналу камери змішувача. Змішання газів, що протікають по камері змішувача, відбувається внаслідок різниці швидкостей закінчення кисню і пального газу.
Довжина шляху змішування і величина розрідження тісно пов'язані з формою і розмірами отворів інжектора, змішувальної камери і вихідних каналів мундштука. Від діаметра отвору інжектора залежить довжина инжектируются поверхні кисневої струменя. Від розмірів змішувальної камери залежить якість змішування газів. Оптимальна довжина шляху змішування газів повинна бути на 15-20% менше довжини циліндричного каналу камери змішувача.
Дифузор - конічна частина камери змішувача, підвищує стабільність процесу інжекції, покращує процес змішування газів і повноту згоряння пального газу. У дифузорі кінетична енергія руху суміші газів перетворюється в потенційну енергію статичного тиску і супроводжується зниженням швидкості і підвищенням тиску газової суміші, під дією якого відбувається її рівномірний витікання з вихідного каналу мундштука. Оптимальний кут дифузора 8 0. при зміні кута в будь-якому напрямку коефіцієнт інжекції різко падає.
Правильно встановлений склад суміші, якісне змішення і стабільне витікання газів з вихідного каналу мундштука є необхідною умовою повного згоряння суміші, рівномірної температури та стійкості полум'я.
Одним з важливих елементів безпечної роботи ризиків є стійкість до зворотних ударів полум'я
Для того щоб уникнути проникнення полум'я всередину різака, визначимо причини, що сприяють виникненню зворотного удару і заходи протидії цьому явищу.
На стійкість горіння полум'я і зміна складу горючої суміші впливають такі чинники:
співвідношення діаметрів отворів інжектора, змішувальної камери і мундштука;
обов'язкова наявність дифузора і конфузора в газовому тракті;
підвищене нагрівання мундштука різака;
різкі перепади тисків газів перед різаком;
конструктивні або виробничі помилки.
Підвищене нагрівання мундштука - основна причина порушення сталості суміші в різаках інжекторного типу. Основною умовою, що забезпечує стійке горіння полум'я, є рівність швидкості витікання і швидкості поширення полум'я горючої суміші у поверхні мундштука на виході з сопла. У центрі струмінь витікає суміші має найбільшу швидкість, а по зовнішньому периметру струменя найменшу. Якщо швидкість витікання горючої суміші у поверхні вихідного сопла мундштука менше швидкості займання, полум'я стає нестійким і проникає всередину сопла (сопел), далі всередину мундштука, що в кінцевому підсумку призводить до проникнення полум'я в різак, тобто до зворотного удару. Швидкість займання і швидкість витікання суміші в значній мірі залежать від температури. З підвищенням температури горючої суміші швидкість займання різко зростає, а швидкість витікання з сопла (сопел) у поверхні мундштука падає изза зростаючого гальмуючого дії нагрітих стінок сопла (сопел) мундштука, незважаючи на розширення газів. Такі умови для проникнення зворотного удару полум'я створюються при нагріванні мундштука до температури: для ацетилено-кисневої суміші - 300400 0. для пропано-кисневої (аналогічно при застосуванні природного газу) - 550 650 0.
Матеріали, наведені в цій статті, спрямовані на те, щоб створити прецедент визначення технологічних можливостей інжекторних різаків, пропонованих на ринку Росії
При досить великому російському ринку ризиків для кисневого різання (орієнтовно 450 тис. Штук на рік) виробники в запалі конкурентної боротьби для зниження витрат при виготовленні продукції найчастіше йдуть на неприпустиме зниження маси деталей або спрощення конструктивних елементів деталей, свідомо погіршуючи технологічні можливості ризиків і їх безпеку .
В даний час кілька підприємств передали в ТОВ «СКТБ АВТОГЕНТЕХМАШ» свої вироби для проведення випробувань. У числі перших завод газозварювального обладнання «Роар» надав кілька серій ризиків торгових марок «РС» і «ДОН». У процесі підготовки статті наша випробувальна лабораторія, яка повністю укомплектована сучасними стендами, провела випробування переданих ризиків на предмет відповідності вимогам ГОСТ 5191. Перевірялися параметри газового тракту, наявність всіх необхідних конструктивних компонентів, якість (шорсткість) поверхонь, що формують газовий тракт, і тільки після цього здійснювалася перевірка параметрів інжекції, витратних параметрів і випробувань на горіння в різних режимах. Особливу увагу було звернуто на безпеку ризиків.
На підставі отриманих результатів ТОВ «СКТБ АВТОГЕНТЕХМАШ» проведе роботу по створенню єдиної для РФ методики випробування газових різаків інжекторного типу і затвердить її в «Ростехнадзоре», а також підготує пропозиції з переробки ГОСТу 5191 на підставі сучасних вимог, що пред'являються до обладнання.
А.К. Нікітін
Генеральний директор
ТОВ «СКТБ АВТОГЕНТЕХМАШ»